Alcast Company Fundamentals Explained
Alcast Company Fundamentals Explained
Blog Article
An Unbiased View of Alcast Company
Table of ContentsThe Buzz on Alcast CompanyWhat Does Alcast Company Mean?More About Alcast CompanySome Known Factual Statements About Alcast Company The Ultimate Guide To Alcast CompanyAn Unbiased View of Alcast Company
The subtle difference hinges on the chemical material. Chemical Contrast of Cast Aluminum Alloys Silicon promotes castability by minimizing the alloy's melting temperature level and boosting fluidity during casting. It plays an essential duty in allowing intricate mold and mildews to be filled up precisely. In addition, silicon adds to the alloy's toughness and wear resistance, making it important in applications where durability is crucial, such as automotive parts and engine components.It also enhances the machinability of the alloy, making it easier to process right into finished products. In this means, iron contributes to the overall workability of light weight aluminum alloys.
Manganese contributes to the toughness of aluminum alloys and improves workability (aluminum casting manufacturer). It is typically used in functioned light weight aluminum products like sheets, extrusions, and accounts. The presence of manganese aids in the alloy's formability and resistance to fracturing throughout construction procedures. Magnesium is a light-weight element that provides stamina and effect resistance to aluminum alloys.
The 8-Minute Rule for Alcast Company
Zinc boosts the castability of aluminum alloys and helps control the solidification procedure throughout spreading. It enhances the alloy's toughness and solidity.
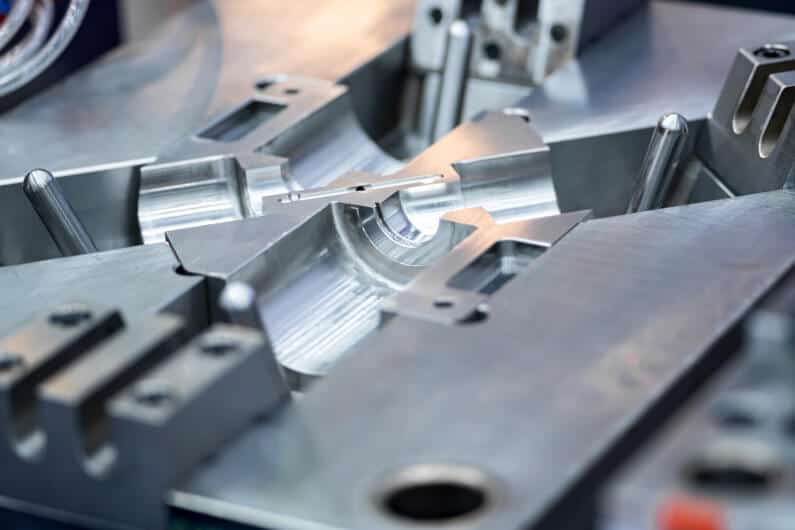
The primary thermal conductivity, tensile stamina, yield strength, and elongation vary. Select suitable raw materials according to the performance of the target product created. Among the above alloys, A356 has the greatest thermal conductivity, and A380 and ADC12 have the most affordable. The tensile limit is the contrary. A360 has the finest yield stamina and the highest prolongation rate.
Alcast Company Fundamentals Explained

In precision casting, 6063 is fit for applications where complex geometries and top notch surface area finishes are extremely important. Examples consist of telecommunication units, where the alloy's exceptional formability permits streamlined and cosmetically pleasing layouts while keeping architectural stability. Likewise, in the Lights Solutions sector, precision-cast 6063 components create elegant and efficient lighting fixtures that require intricate shapes and great thermal efficiency.
The A360 shows exceptional elongation, making it excellent for facility and thin-walled elements. In precision spreading applications, A360 is well-suited for sectors such as Customer Electronics, Telecommunication, and Power Devices.
Alcast Company for Dummies
Its special residential or commercial properties make A360 a useful selection for accuracy casting in these industries, boosting product toughness and high quality. Casting Foundry. Light weight aluminum alloy 380, or A380, is a commonly used spreading alloy with numerous distinct attributes.
In accuracy casting, aluminum 413 beams in the Consumer Electronic Devices and Power Devices markets. This alloy's exceptional corrosion resistance makes it an excellent choice for outside applications, ensuring durable, long lasting items in the mentioned markets.
Our Alcast Company PDFs
The light weight aluminum alloy you pick will substantially impact both the spreading process and the residential or commercial properties of the last product. Due to the fact that of this, you must make your choice carefully and take an informed strategy.
Figuring out one of the most ideal aluminum alloy for your application will indicate weighing a broad variety of characteristics. These comparative alloy qualities adhere to the North American Die Casting Association's guidelines, and we've separated them into two classifications. The initial classification addresses alloy qualities that affect the manufacturing process. The 2nd covers characteristics impacting the residential or commercial properties of the last product.
Top Guidelines Of Alcast Company
The alloy you select for die casting straight influences a number of aspects of the casting process, like how very easy the alloy is to deal with and if it is susceptible to casting flaws. Hot breaking, likewise referred to as solidification fracturing, is a typical die casting problem for light weight aluminum alloys that can cause inner or surface-level rips or splits.
Particular aluminum alloys are much more prone to warm splitting than others, and your option needs to consider this. An additional typical issue found in the die spreading of aluminum is die soldering, which is when the cast adheres to the die walls and read review makes ejection hard. It can damage both the actors and the die, so you ought to look for alloys with high anti-soldering properties.
Rust resistance, which is currently a remarkable quality of light weight aluminum, can differ significantly from alloy to alloy and is a necessary characteristic to consider relying on the ecological problems your item will be revealed to (Aluminum Castings). Wear resistance is another residential or commercial property commonly sought in light weight aluminum items and can differentiate some alloys
Report this page